PERFORMAX INTERNATIONAL CONVERSION TECHNOLOGY
Performax International’s market leading reputation for right-hand drive conversions stems from its investment in advanced design and manufacturing technologies employed by all OEM manufacturers. Performax International achieves 100% traceability of all parts by means of a comprehensive part numbering system including batch tracking. The components designed and manufactured as part of the conversion process are modelled from 3D laser scanned data or altered directly from OEM 3D models. Prototypes of these models are manufactured using various prototyping technologies, the most common of which is 3D printing. These 3D printed parts are test fitted in vehicles to ensure correct fit and function before releasing the part for manufacture.
3D LASER SCANNERS
Kreon Technologies 3D laser scanner can reproduce a digital model of any part down to an accuracy of 0.025mm, less than half the width of a human hair.
These scanners are designed to quickly and accurately capture 3D data of objects and environments, and they can be used in a variety of applications such as reverse engineering, quality control, and 3D modelling.
Kreon 3D scanners use advanced laser technology to capture high-resolution 3D data, and they are known for their speed and accuracy. They also come with a range of software tools that allow users to process and analyse the data captured by the scanner, making it easy to create detailed 3D models and CAD files.
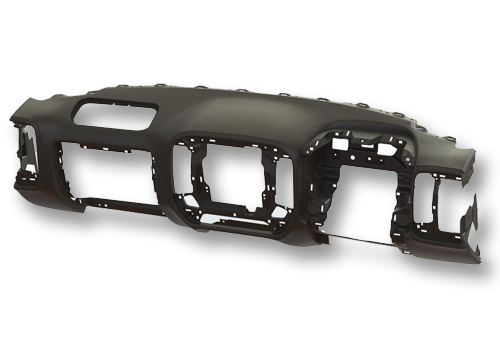
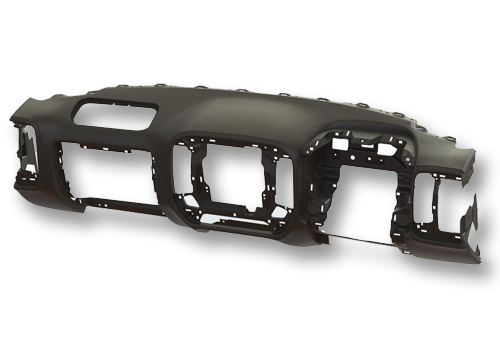
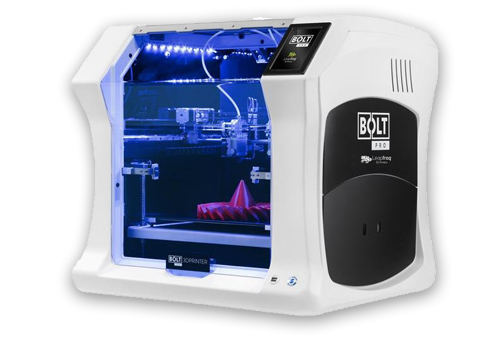
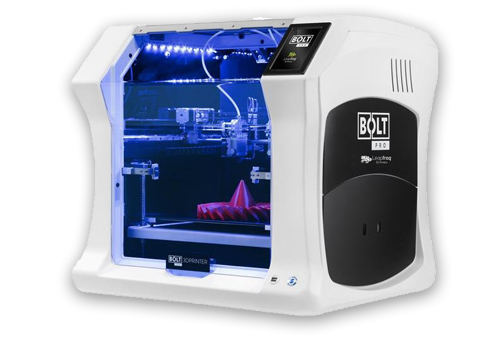
3D PRINTING CUSTOM VEHICLE PART
The Leapfrog Bolt Pro 3D Printer is a highly advanced dual filament 3D printing solution, renowned for its exceptional capabilities and versatility. This state-of-the-art printer is employed by industry giants such as Rolls Royce and Volkswagen, underscoring its reliability and superior performance in professional applications. The Bolt Pro's ability to handle dual filaments simultaneously significantly expands the range of materials and colors that can be used in a single print, making it ideal for creating complex prototypes and parts.
Designed to accommodate large-scale prints, the Bolt Pro is one of the most spacious 3D printers available. This generous build volume is crucial for industries that require the creation of large parts or multiple components in a single print run, enhancing efficiency and reducing production time. Its high-speed printing capabilities allow for rapid prototyping and quick iteration of parts, ensuring the best possible fit and function before moving into full-scale production, which is invaluable in the automotive and aerospace industries.
HIGH PRESSURE INJECTION MOULDING
Our interior plastics are reproduced using the same manufacturing method as OEM manufacturers.
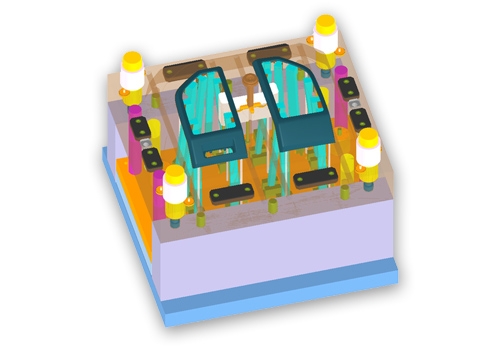
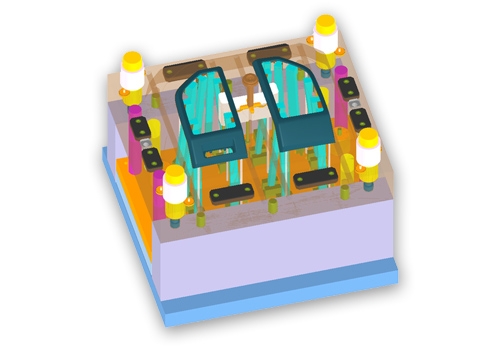
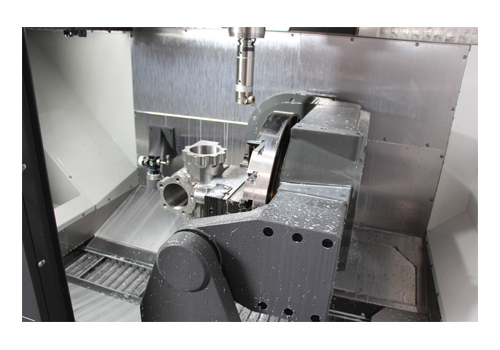
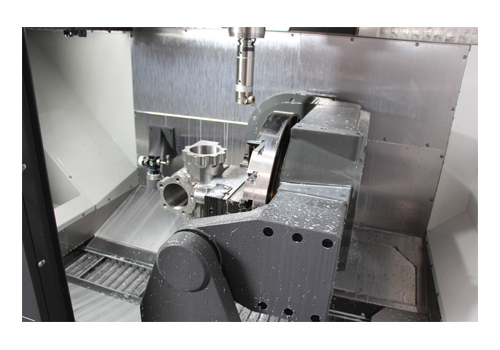
5-AXIS UNIVERSAL MACHINING CENTRE
A Haas UMC750-SS universal machining centre as used by Triple Eight Race Engineering provides precision machining of high tolerance parts such as steering components, with a positioning resolution of down to 0.001mm.
VACUUM FORMING
A Formech vacuum former as used by Dyson, NIKE, and Volkswagen, allows rapid and consistent manufacture of durable plastic components used throughout the conversion process.
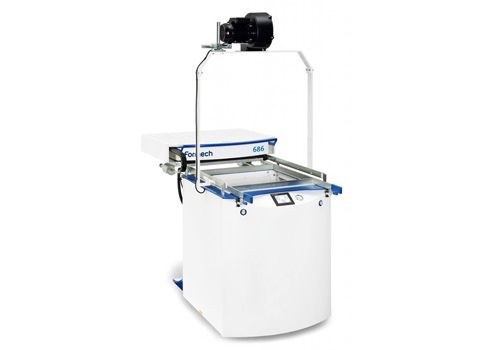
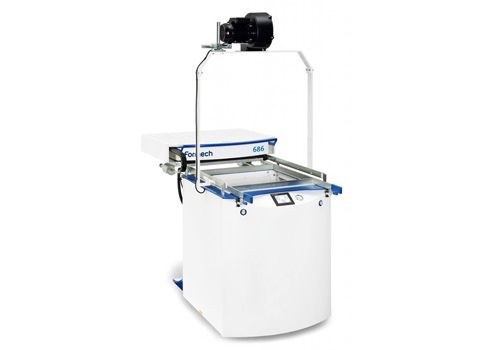
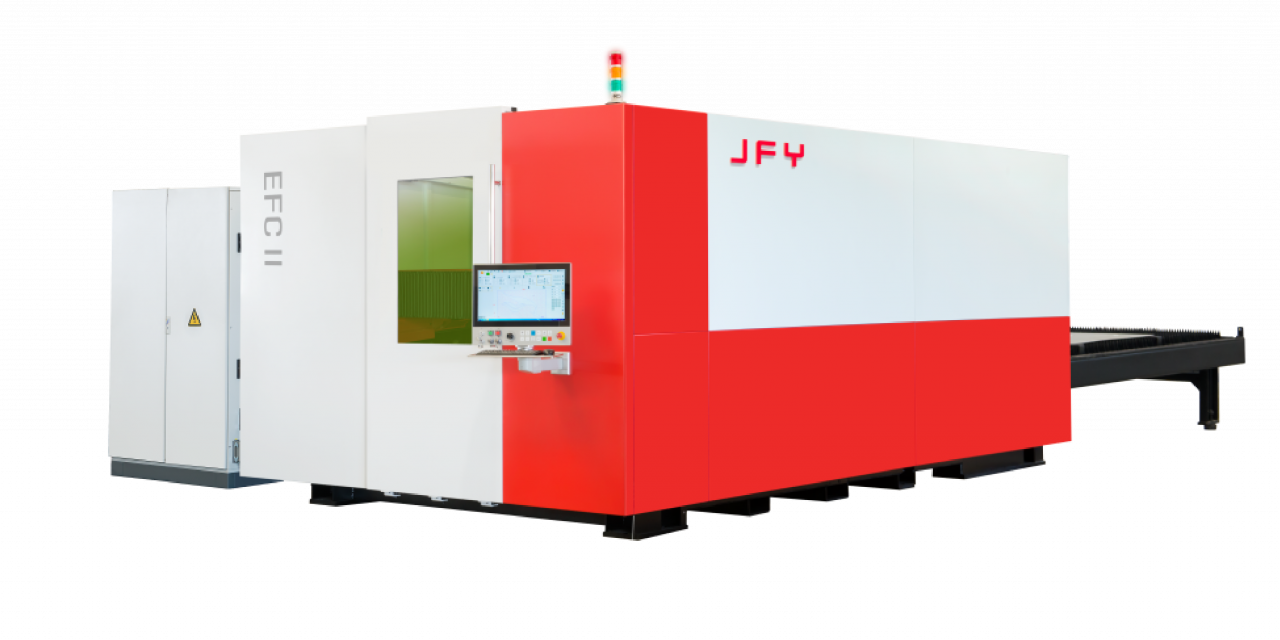
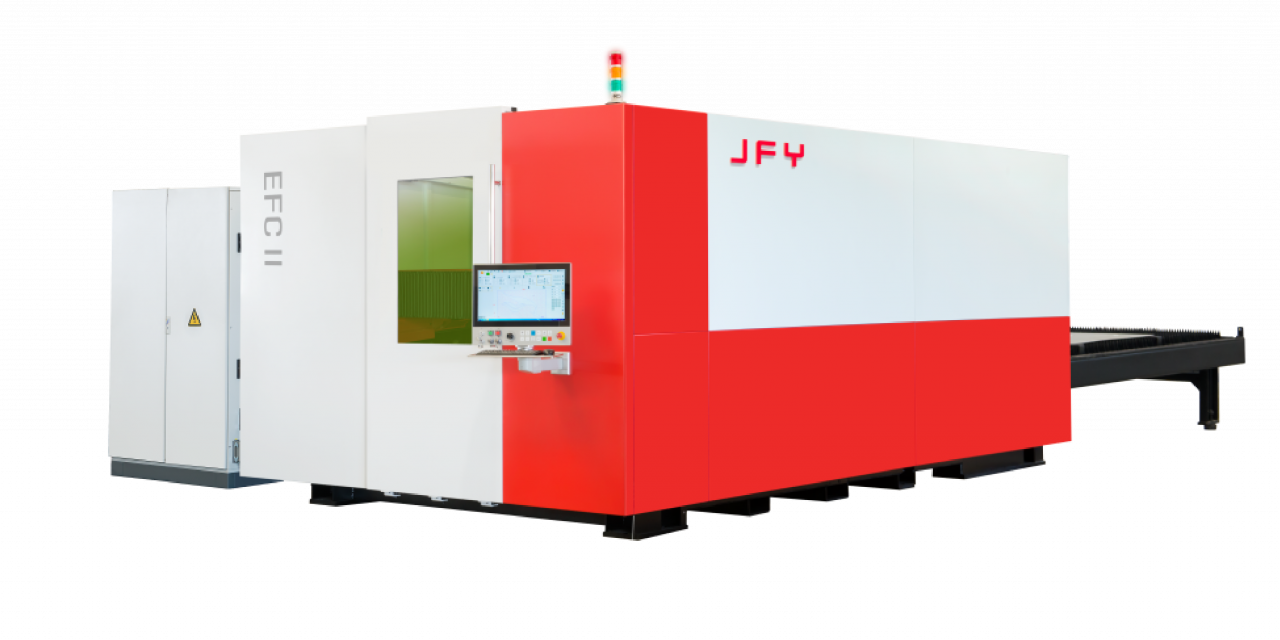
LASER CUTTING MACHINE
The JFY TFC 3015 uses advanced laser technology to cut various metals with precision. It has a large cutting area of 3000mm x 1500mm and can cut up to 20mm steel and 10mm aluminium with 3kW of power. It is fast and efficient, with options for automation and software control. The machine finds applications in industries like metal fabrication, signage, automotive, and aerospace.